The goal of the Nondestructive Evaluation (NDE) laboratory is to introduce ET students to methods and techniques of NDE of parts and materials. Students learn the physical principles and fundamentals of ultrasound material characterization. Students also learn industrial applications of NDE techniques and procedures and become familiar with detection and characterization of defects in materials, such as flaws and cracks. These techniques are studied through experiments that closely simulate industry-relevant manufacturing and testing processes in petrochemical, aerospace, nuclear, railroad, and renewable energy applications using an in-depth case study approach.
The NDE laboratory serves as a training center for undergraduate ET students, as well as for the workforce of companies, such as Boeing, MISTRAS/CONAM, Lockheed Martin, and PECO Energy. The establishment of a state-of-the art laboratory for NDE purposes allows Drexel and its community-college partners to develop training options for technicians located in the region’s key industries.
NDE curriculum is designed to fulfill Levels I & II NDE in theory and training requirements, according to American Society for Nondestructive Testing (ASNT) Recommended Practice.
Development of this laboratory was supported by the NSF Grant # 0632734 “Implementation of the Internet-Based Nondestructive Evaluation Laboratory for Engineering Technology Curriculum.
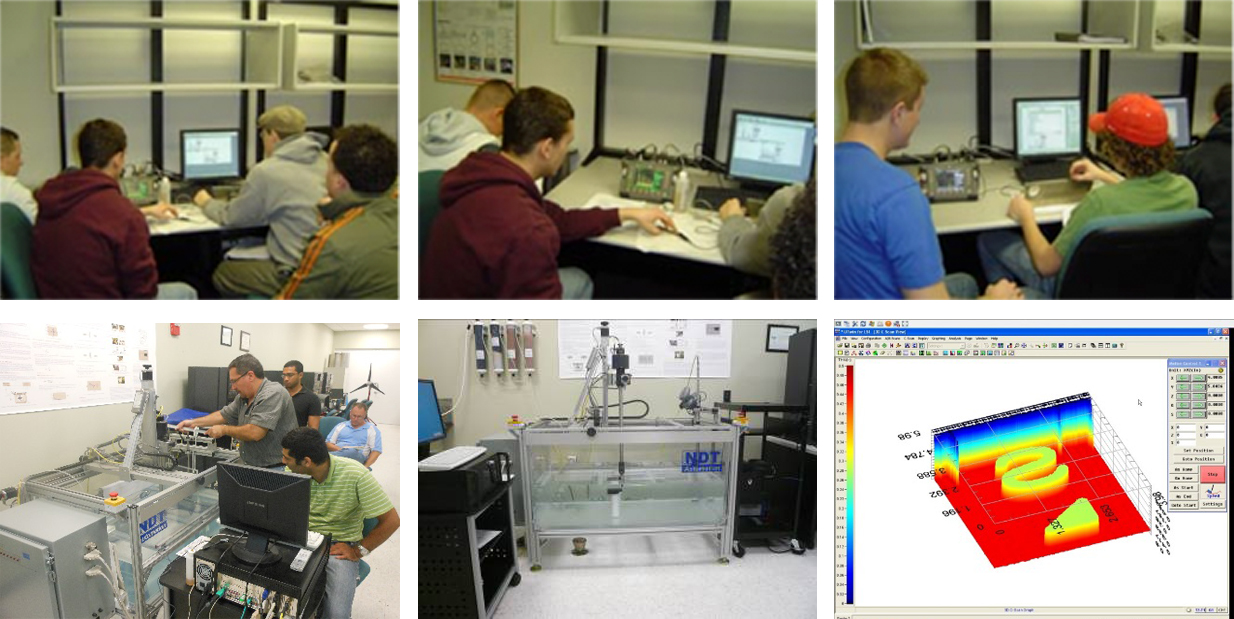
ULTRAPAC II automatic water tank-based system:
Measurements of the sound velocity, attenuation coefficients, and evaluation of properties of piezoelectric transducers are carried out using ULTRAPAC II automatic water tank-based system. The placement of the transducers and data collection are controlled by the UTwinTM software. The system can be controlled by the local or remote computers via Internet. The Internet-based remote operation of the ULTRAPAC II water-tank-based system is controlled by the ultrasonic C-scan software. The system allows for obtaining a plain view of the test object. Variations in color represent the depth of the reflectors on the 3-D image in the test object.